Benefits of Lean Construction Principles
Lean construction principles offer numerous advantages to the construction industry. One key benefit is the reduction of waste throughout projects, leading to increased efficiency and cost savings. By focusing on value-adding activities and streamlining processes, lean construction helps to improve project timelines and overall productivity.
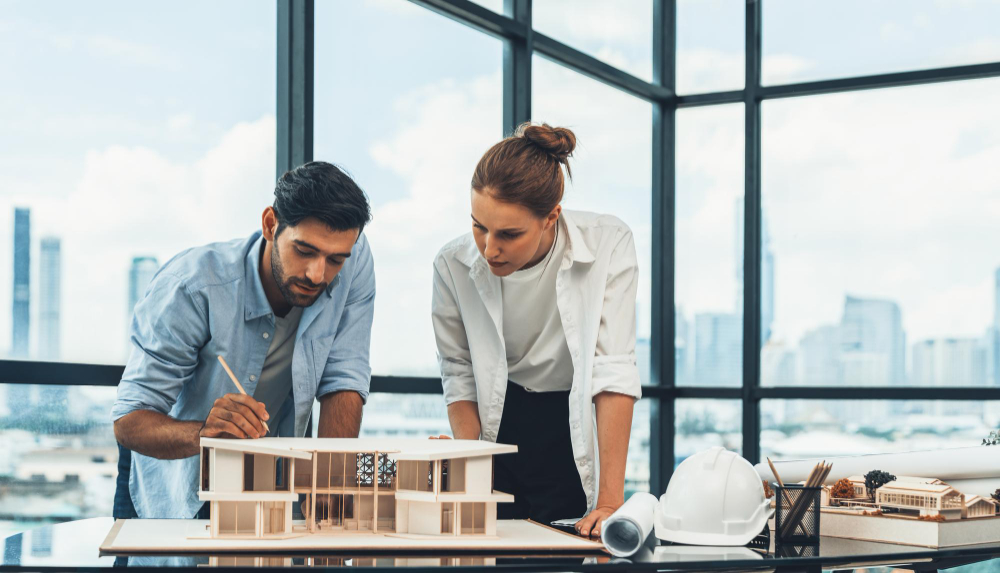
Additionally, implementing lean principles fosters better collaboration and communication among project teams, which results in smoother workflows and enhanced project outcomes. The emphasis on continuous improvement and learning from past experiences allows construction companies to adapt quickly to changing circumstances and deliver projects more effectively.
Key Components of Lean Construction
Lean construction is a method that emphasizes efficiency and productivity in the construction industry. One key component of this approach is the management of project flow to optimize resources and minimize waste. By focusing on the smooth progression of tasks from start to finish, lean construction aims to deliver projects on time and within budget.
Another essential component of lean construction is the continuous improvement mindset. This involves constantly seeking ways to streamline processes, enhance communication, and achieve better results. By fostering a culture of learning and adaptation, lean construction teams can respond effectively to challenges and deliver high-quality projects that meet or exceed client expectations.
Principles of Value Stream Mapping in Construction
Value Stream Mapping (VSM) in construction is a powerful tool that enables teams to visualize and analyze the flow of materials, information, and processes within a construction project. By creating a visual representation of the current state and future state of the project, VSM helps identify inefficiencies, bottlenecks, and opportunities for improvement. This allows for better coordination and communication among team members, leading to increased productivity and reduced waste in construction projects.
One key principle of Value Stream Mapping in construction is to focus on the value-adding activities that contribute to the final product or service. By identifying and prioritizing these activities, project teams can streamline their processes and eliminate non-value adding tasks that consume time and resources. Through the use of VSM, construction teams can optimize their workflows, improve project delivery times, and enhance overall project quality.
Eliminating Waste in Construction Projects
Construction projects are often plagued by various types of waste that can hinder productivity and efficiency. One common form of waste is overproduction, where excess materials are ordered or work is done ahead of schedule, leading to unnecessary costs and delays. Transportation waste is another issue, occurring when materials are moved around the site inefficiently, resulting in extra time and resources being wasted. By identifying and eliminating these inefficient practices, construction projects can streamline their processes and reduce unnecessary waste.
Another form of waste commonly seen in construction projects is waiting time, which occurs when workers are idle due to poor planning or coordination. This downtime can lead to project delays and increased costs, highlighting the importance of efficient scheduling and communication among team members. Moreover, defects in workmanship or materials can also contribute to waste, requiring rework and additional resources to rectify issues that could have been prevented with proper quality control measures in place. By addressing these sources of waste, construction projects can improve their overall efficiency and deliver higher quality outcomes.
Importance of Continuous Improvement in Lean Construction
Continuous improvement is a cornerstone of lean construction, emphasizing the ongoing quest for efficiency and excellence in project delivery. By continually seeking ways to enhance processes, reduce waste, and optimize resources, construction teams can drive productivity and deliver high-quality results to clients. Through a commitment to incremental enhancements and a culture of learning and innovation, lean construction fosters a proactive approach to project management that prioritizes adaptability and refinement.
The importance of continuous improvement in lean construction is underscored by its ability to drive competitive advantage and sustainable growth in the construction industry. By encouraging a mindset of continuous learning and development among project teams and stakeholders, lean principles empower organizations to evolve and stay ahead in a dynamic market environment. Through a structured approach to refining processes, addressing challenges, and capitalizing on opportunities, continuous improvement serves as a catalyst for driving operational efficiency and achieving project success.
Implementing Pull Planning in Construction Projects
Pull planning is a key aspect of lean construction methodology that focuses on coordinating tasks based on actual project needs rather than preset schedules. By involving all stakeholders in the planning process, pull planning aims to enhance collaboration, communication, and efficiency throughout the construction project. This approach helps in identifying constraints, minimizing delays, and improving the overall workflow by streamlining activities in a synchronized manner.
Through pull planning, project teams can visualize the workflow, identify potential bottlenecks, and make real-time adjustments to ensure smoother project execution. By breaking down the project into smaller work packages and determining the sequence of activities based on their interdependencies, teams can achieve better coordination and alignment towards common project goals. This proactive planning approach not only enhances transparency and accountability but also promotes a culture of continuous improvement within the construction project.
Using Last Planner System for Lean Construction
The Last Planner System (LPS) is a collaborative approach that aims to enhance production planning in construction projects. It involves the last planners, typically the foremen or subcontractors, actively engaging in the planning process to increase efficiency and productivity. Through a series of weekly coordination meetings, the last planners discuss potential constraints, work sequences, and any necessary adjustments to the plan to ensure smooth project flow.
One key aspect of the Last Planner System is the commitment to reliable promises. By setting realistic and achievable goals for each phase of the project, team members are held accountable for their commitments. This helps in fostering transparency, improving communication, and ultimately leading to a more synchronized and streamlined construction process. By involving those closest to the work in the planning stages, the Last Planner System empowers team members to take ownership of their tasks and make informed decisions to drive successful project outcomes.
Strategies for Improving Communication in Lean Construction
Effective communication is crucial in lean construction projects to ensure that all team members are aligned and working towards the same goals. One strategy for improving communication is to hold regular meetings where project updates and challenges are discussed openly. These meetings create transparency and foster collaboration among team members, leading to better problem-solving and decision-making.
Another way to enhance communication in lean construction is to utilize digital collaboration tools. Using platforms that allow for real-time communication and document sharing can streamline processes and ensure that everyone has access to the most up-to-date information. By leveraging technology, project teams can improve efficiency, reduce errors, and enhance overall project outcomes.
Utilizing Technology for Lean Construction Practices
Technological advancements have been instrumental in enhancing lean construction practices. The integration of Building Information Modeling (BIM) software allows for improved visualization, collaboration, and planning in construction projects. BIM facilitates the creation of 3D models that provide a holistic view of the project, enabling stakeholders to identify potential issues early on and make informed decisions to optimize construction processes.
Furthermore, the adoption of mobile applications and project management software streamlines communication and enhances efficiency on construction sites. These tools enable real-time collaboration, access to project data, and instant communication among team members regardless of their location. By leveraging technology, lean construction practices can be further enhanced to minimize waste, improve productivity, and deliver projects on time and within budget.
• Building Information Modeling (BIM) software allows for improved visualization, collaboration, and planning in construction projects
• BIM facilitates the creation of 3D models that provide a holistic view of the project
• Mobile applications and project management software streamline communication and enhance efficiency on construction sites
• Real-time collaboration, access to project data, and instant communication among team members are enabled by these tools
• Technology can help minimize waste, improve productivity, and deliver projects on time and within budget in lean construction practices.
Measuring Performance in Lean Construction
Metrics play a significant role in assessing the efficiency and effectiveness of lean construction projects. By establishing key performance indicators (KPIs) at various stages of the project, teams can track progress, identify potential bottlenecks, and make informed decisions to enhance productivity. These metrics could include cycle time, lead time, adherence to schedules, rework rates, and customer satisfaction levels, providing a comprehensive view of project performance.
Through the continuous monitoring and analysis of these performance metrics, project managers can gain insights into the overall health of the project, enabling them to proactively address issues and optimize processes for improved outcomes. Moreover, measuring performance in lean construction not only facilitates project success but also fosters a culture of accountability and continuous improvement within the project team, ultimately driving higher levels of efficiency and quality in project delivery.
Challenges of Implementing Lean Construction Principles
One of the main hurdles in implementing lean construction principles lies in changing the traditional mindset and practices deeply rooted in the construction industry. Resistance to adopt new methods and a lack of awareness about the benefits of lean practices can hinder the successful implementation of lean construction principles. Additionally, the fragmented nature of the construction industry, with various stakeholders and subcontractors involved in a project, can make it challenging to align everyone towards a common goal of lean practices.
Another challenge in implementing lean construction principles is the dynamic and unpredictable nature of construction projects. Fluctuating project scopes, changing requirements, and unforeseen issues can disrupt the flow of work and impact the efficiency of lean practices. Maintaining a continuous improvement mindset amidst such uncertainties and ensuring all team members are on board with lean principles can pose significant challenges in the implementation process.
Case Studies of Successful Lean Construction Projects
Lean construction principles have been proven effective in various construction projects across different industries. For example, a recent case study showcased how a large commercial building project was completed ahead of schedule and under budget by implementing lean practices. By fostering collaboration among team members, optimizing processes, and continuously improving workflows, the project was able to achieve high efficiency and quality outcomes.
In another successful lean construction project, a renovation of an existing facility was completed with minimal disruptions and cost savings. Through the use of value stream mapping and eliminating waste through streamlined processes, the project team was able to enhance communication and coordination, resulting in improved productivity and overall project success. Such case studies serve as compelling evidence of the tangible benefits that can be achieved by embracing lean construction principles in modern project management strategies.
Future Trends in Lean Construction Industry
As the construction industry continues to evolve, future trends in lean construction are likely to focus on further integration of technology to streamline processes and enhance efficiency. Utilizing advanced tools such as Building Information Modeling (BIM), drones, and project management software will enable teams to collaborate more effectively and make data-driven decisions that ultimately lead to improved project outcomes.
Moreover, the adoption of sustainable and environmentally friendly practices is expected to become increasingly important in lean construction. Implementing green building techniques, using recycled materials, and reducing carbon footprints are key aspects that align with the principles of lean construction while meeting the growing demand for eco-conscious construction practices. By incorporating sustainability into lean construction initiatives, the industry can not only achieve cost savings but also contribute to a more environmentally responsible approach to building projects.
Additional Resources:
[catlist categorypage=”yes”]
[newsletter]
Table of Contents
Categories:
[categories orderby=name]
Latest Posts:
[sbs_latest_posts]
FAQs:
What are the benefits of lean construction principles?
Lean construction principles help improve efficiency, reduce waste, increase productivity, and enhance collaboration among project teams.
What are the key components of lean construction?
The key components of lean construction include value stream mapping, eliminating waste, continuous improvement, pull planning, last planner system, improved communication, use of technology, and performance measurement.
How can value stream mapping be used in construction projects?
Value stream mapping in construction helps identify and eliminate non-value added activities, streamline processes, and improve overall project efficiency.
How can waste be eliminated in construction projects?
Waste in construction projects can be eliminated by identifying and reducing activities that do not add value to the project, such as overproduction, waiting time, excess inventory, unnecessary movement, defects, and underutilized talent.
Why is continuous improvement important in lean construction?
Continuous improvement in lean construction helps project teams learn from past experiences, identify areas for improvement, and implement changes to enhance project performance over time.
How can pull planning be implemented in construction projects?
Pull planning in construction involves scheduling work based on when it is needed, rather than based on a predetermined timeline. This helps minimize delays, improve coordination, and increase project efficiency.
What is the last planner system and how is it used in lean construction?
The last planner system is a collaborative approach to project planning that involves input from all project team members. It helps improve communication, coordination, and accountability among team members.
How can communication be improved in lean construction projects?
Communication in lean construction projects can be improved by implementing strategies such as regular team meetings, clear communication channels, and using collaborative tools and technology.
How can technology be utilized in lean construction practices?
Technology can be used in lean construction practices for project scheduling, collaboration, data analysis, virtual modeling, and communication to improve project efficiency and productivity.
How is performance measured in lean construction projects?
Performance in lean construction projects can be measured using key performance indicators (KPIs) such as project cost, schedule adherence, quality metrics, safety records, and customer satisfaction.
What are some challenges of implementing lean construction principles?
Challenges of implementing lean construction principles include resistance to change, lack of buy-in from project teams, limited resources, cultural barriers, and difficulty in measuring the impact of lean practices.
Can you provide examples of successful lean construction projects?
Case studies of successful lean construction projects include the Toyota Production System, Lean Project Delivery System, Lean Construction Institute projects, and various construction projects that have improved efficiency and reduced waste through lean practices.
What are some future trends in the lean construction industry?
Future trends in the lean construction industry may include further adoption of technology, increased focus on sustainability, integration of lean principles in prefabrication and modular construction, and continued emphasis on collaboration and continuous improvement within project teams.