Benefits of Prefabrication in Construction
Prefabrication in construction offers numerous benefits that can significantly improve efficiency and project timelines. One key advantage is the reduced construction time on site, as components are manufactured off-site and then assembled quickly at the project location. This streamlined process can lead to faster project completion, allowing for quicker occupancy or opening of the structure.
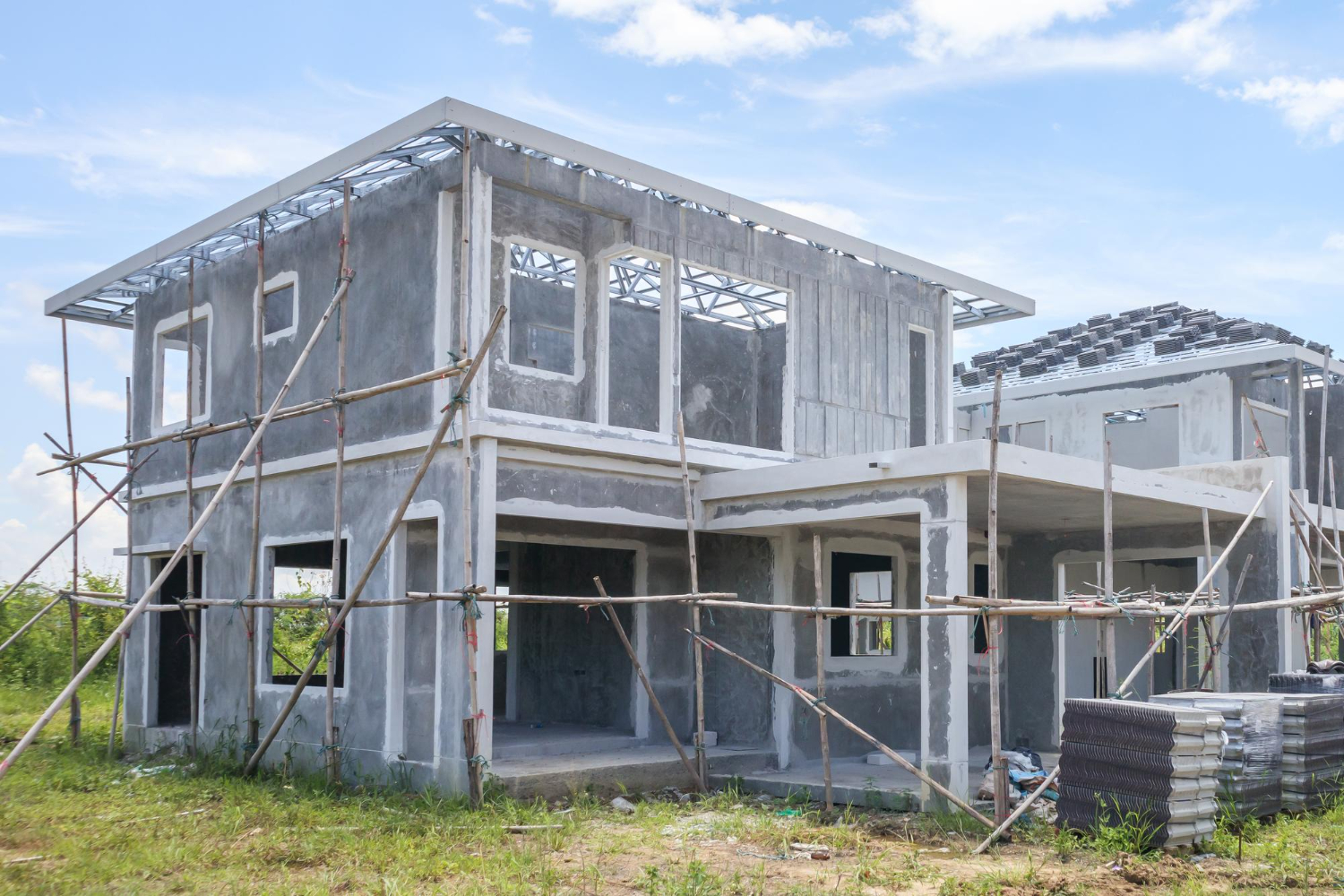
Additionally, prefabrication often results in lower overall costs due to decreased labor requirements, minimized material waste, and optimized construction schedules. The controlled environment of the factory where components are fabricated also enhances quality control, leading to higher precision and consistency in the final construction. Ultimately, the benefits of prefabrication in construction extend beyond just speed and cost savings, impacting project quality and performance as well.
Types of Prefabricated Construction Methods
There are several types of prefabricated construction methods commonly used in the industry. One method is modular construction, where entire sections of a building are constructed off-site in a factory and then transported to the construction site for assembly. This method allows for greater precision and quality control, as the modules are built in a controlled environment. Panelized construction is another method, where wall panels are prefabricated off-site and then delivered to the construction site for installation. This method can speed up the construction process and reduce on-site labor requirements.
Environmental Impact of Prefabrication
Prefabrication in construction offers various environmental benefits. One of the primary advantages is the reduction of waste generated at construction sites. With prefabricated construction methods, materials are precisely cut and assembled off-site, minimizing the amount of onsite wastage. This efficiency not only contributes to a cleaner worksite but also helps in conserving natural resources.
Additionally, prefabrication can lead to lower energy consumption during the construction process. The controlled environment of a factory setting allows for better management of resources such as energy and water, leading to reduced energy usage compared to traditional construction methods. Moreover, the transportation of prefabricated components to the construction site is often more streamlined, resulting in lower emissions and less impact on the surrounding environment.
Cost Savings with Prefabricated Construction
Cost savings are a significant advantage of prefabricated construction methods. With prefabrication, the majority of construction work is done off-site in a controlled environment, which can lead to increased efficiency and reduced labor costs. Additionally, the use of standardized components in prefabrication can help streamline the construction process, resulting in time savings and ultimately cost savings for the project.
Furthermore, prefabrication allows for better cost predictability and control. By manufacturing components in a factory setting, builders can more accurately estimate material usage, labor costs, and project timelines. This increased predictability can help project managers allocate resources more effectively and mitigate the risk of cost overruns that are common in traditional on-site construction projects.
Challenges and Limitations of Prefabrication
One of the key challenges in prefabricated construction is the potential for transport and logistics issues. Moving pre-assembled components from the manufacturing facility to the construction site can be complex and may require careful planning to ensure timely delivery and avoid any damage during transportation. Additionally, the size and weight of prefabricated elements can also pose challenges in terms of maneuvering them into place on-site, especially in urban areas with limited space.
Another limitation of prefabrication is the restricted design flexibility compared to traditional construction methods. Prefabricated components are often produced in standard sizes and shapes, which can limit architectural creativity and customization. This constraint may not be suitable for projects that require unique or intricate designs that go beyond the capabilities of prefabricated elements. Therefore, striking a balance between the benefits of factory-controlled production and design flexibility is crucial in successfully implementing prefabricated construction techniques.
Innovations in Prefabricated Construction
Advancements in technology have revolutionized the prefabricated construction industry, leading to innovative methods that enhance efficiency and precision. One such innovation is the use of Building Information Modeling (BIM) software, which allows for detailed planning and visualization of a project before fabrication begins. This technology enables coordination between different trades, streamlining the construction process and minimizing errors.
Another notable innovation is the development of robotic construction systems that automate tasks such as welding, cutting, and assembling components. These robotic systems can work with high precision and speed, reducing labor costs and improving the overall quality of the prefabricated elements. Additionally, the integration of augmented reality and virtual reality tools has facilitated better communication among project teams and stakeholders, allowing for real-time collaboration and visualization of the final product.
Quality Control in Prefabricated Construction
Quality control in prefabricated construction is crucial to ensure that the components and modules are constructed to meet the required standards and specifications. This process involves rigorous checks and inspections at various stages of fabrication to identify and rectify any defects or deviations from the design. By implementing strict quality control measures, prefabricated construction projects can maintain consistency in the production process and deliver high-quality buildings to clients.
One of the key aspects of quality control in prefabricated construction is the use of standardized procedures and protocols to minimize errors and improve efficiency. This includes adopting advanced technologies such as Building Information Modeling (BIM) to create detailed digital representations of the project and identify any potential issues before they arise. Additionally, regular testing and monitoring of materials and components help to ensure that the final product meets all safety and performance requirements.
Safety Considerations in Prefabricated Construction
One key safety consideration in prefabricated construction is ensuring proper handling and transportation of prefabricated components. These components are often large and heavy, requiring specialized equipment and trained personnel to maneuver them safely. Inadequate handling procedures can lead to accidents, injuries, and damage to the prefabricated elements, causing delays and added costs to the project.
Additionally, site safety during the assembly and installation of prefabricated components is crucial. Workers must follow proper safety protocols, including wearing appropriate personal protective equipment and adhering to strict safety guidelines. Assembling prefabricated elements at great heights or in confined spaces can pose additional risks, making it essential for workers to be vigilant and well-trained to prevent accidents and ensure a safe working environment.
Future Trends in Prefabricated Construction
Increasing automation and digitalization are expected to play a significant role in the future of prefabricated construction. Technologies such as Building Information Modeling (BIM), 3D printing, and robotics are likely to streamline processes, improve precision, and reduce construction timelines. Additionally, the integration of smart technologies and Internet of Things (IoT) solutions in prefabricated construction is set to enhance the efficiency and sustainability of buildings.
Another emerging trend in prefabricated construction is the focus on creating more sustainable and energy-efficient buildings. With a growing awareness of environmental concerns and the need to reduce carbon emissions, prefabricated construction methods that prioritize eco-friendly materials, energy-efficient designs, and renewable energy sources are gaining traction. The use of green building certifications and sustainable construction practices is becoming increasingly important in the industry, driving the development of prefabricated solutions that align with these principles.
Case Studies of Successful Prefabricated Projects
In recent years, the construction industry has witnessed an increase in successful prefabricated projects that showcase the benefits of this off-site construction method. One notable case study is the Barcelona Housing Systems project in Spain, where prefabricated modules were used to construct affordable housing units efficiently and sustainably. The project demonstrated how prefabrication can streamline the construction process while maintaining high-quality standards.
Another remarkable example is the Park Avenue Skyscraper project in New York City, where prefabricated components were utilized to build a 50-story tower in record time. This project highlighted the speed and cost-effectiveness of prefabrication, as well as its ability to meet the demands of complex urban environments. These case studies underscore the potential of prefabricated construction to revolutionize the industry and pave the way for more innovative and sustainable building practices.
Comparing Traditional Construction Methods with Prefabrication
Traditional construction methods often involve on-site building processes where materials are delivered to the location and assembled from scratch. This method requires skilled labor, coordination between different trades, and can be subject to weather delays. In contrast, prefabrication involves manufacturing building components in a controlled environment before transporting them to the site for assembly. This technique reduces construction time, improves quality control, and minimizes on-site labor requirements.
One key difference between traditional construction and prefabrication is the level of customization available. Traditional methods allow for more flexibility in design changes during construction, while prefabrication typically requires adherence to standardized modules. Despite this limitation, prefabrication offers more consistency in product quality, as components are manufactured following strict guidelines. Additionally, prefabrication often leads to reduced waste generation and a more efficient use of materials compared to traditional construction methods.
• Traditional construction methods involve on-site building processes
• Requires skilled labor and coordination between different trades
• Subject to weather delays
• Prefabrication involves manufacturing building components in a controlled environment before transporting them to the site for assembly
• Reduces construction time and improves quality control
• Minimizes on-site labor requirements
One key difference between traditional construction and prefabrication is the level of customization available:
– Traditional methods allow for more flexibility in design changes during construction
– Prefabrication typically requires adherence to standardized modules
Despite limitations in customization, prefabrication offers benefits such as:
– Consistency in product quality due to strict guidelines followed during manufacturing
– Reduced waste generation and more efficient use of materials compared to traditional construction methods
Regulatory Standards for Prefabricated Construction
When it comes to prefabricated construction, adherence to regulatory standards is crucial to ensure the safety and quality of the built environment. Regulatory bodies set guidelines and codes that govern different aspects of prefabricated construction, including structural integrity, fire safety, energy efficiency, and environmental impact. These standards help to streamline the construction process, minimize risks, and ensure that prefabricated structures meet the required safety and performance criteria.
Compliance with regulatory standards also helps to foster trust and confidence among stakeholders, including clients, architects, engineers, contractors, and regulatory authorities. By following established regulations and codes, prefabricated construction projects can proceed smoothly and efficiently, with reduced chances of delays, disputes, or safety incidents. Moreover, adherence to regulatory standards demonstrates a commitment to upholding best practices in construction, which can enhance the reputation and credibility of prefabricated construction companies in the industry.
Training and Education in Prefabricated Construction
Training and education play a crucial role in ensuring the successful implementation of prefabricated construction methods. Workers need to be equipped with the necessary skills and knowledge to effectively work with prefabricated components and assemblies. This includes understanding how to handle and install prefabricated elements correctly to ensure structural integrity and adherence to design specifications.
Moreover, training programs can also focus on promoting innovation and efficiency in prefabricated construction processes. By educating workers on the latest advancements and techniques in the industry, companies can improve productivity and quality while reducing construction time and costs. Continued education and training are essential to keep up with the evolving nature of prefabricated construction and to ensure that projects are completed to the highest standards.
Additional Resources:
[catlist categorypage=”yes”]
[newsletter]
Table of Contents
Categories:
[categories orderby=name]
Latest Posts:
[sbs_latest_posts]
FAQs:
What are the benefits of using prefabrication in construction?
Prefabrication in construction offers benefits such as faster project completion, reduced on-site labor requirements, improved quality control, and cost savings.
What are the different types of prefabricated construction methods?
Some common types of prefabricated construction methods include modular construction, panelized construction, and volumetric construction.
How does prefabrication impact the environment?
Prefabrication can be more sustainable than traditional construction methods as it often results in less waste generation, reduced energy consumption, and lower carbon emissions.
How can prefabricated construction lead to cost savings?
Prefabricated construction can lead to cost savings through reduced labor costs, faster project completion times, and minimized material waste.
What are some challenges and limitations of using prefabrication in construction?
Challenges of prefabrication include transportation and logistics issues, limitations in customization, and potential quality control concerns.
What innovations are being made in prefabricated construction?
Innovations in prefabricated construction include advancements in technology, such as Building Information Modeling (BIM), as well as the use of sustainable materials and construction methods.
How is quality control maintained in prefabricated construction?
Quality control in prefabricated construction is often ensured through strict manufacturing standards, rigorous inspection processes, and adherence to regulatory guidelines.
What safety considerations should be taken into account in prefabricated construction?
Safety considerations in prefabricated construction include proper handling of prefabricated components, adherence to safety protocols during assembly, and ensuring structural integrity.
What are some future trends to look out for in prefabricated construction?
Future trends in prefabricated construction may include increased use of automation, off-site manufacturing facilities, and advancements in sustainable building practices.
Can you provide some examples of successful prefabricated projects?
Some successful prefabricated projects include the One Central Park in Sydney, Australia, and the Barclays Center in Brooklyn, New York.
How does traditional construction methods compare to prefabrication?
Traditional construction methods typically involve on-site assembly of components, while prefabrication involves the off-site manufacturing of building elements before assembly on-site.
What regulatory standards govern prefabricated construction?
Regulatory standards for prefabricated construction vary by location but often include building codes, zoning regulations, and industry-specific guidelines.
What training and education opportunities are available in prefabricated construction?
Training and education programs in prefabricated construction may include certification courses, workshops, online resources, and hands-on training sessions for industry professionals.